
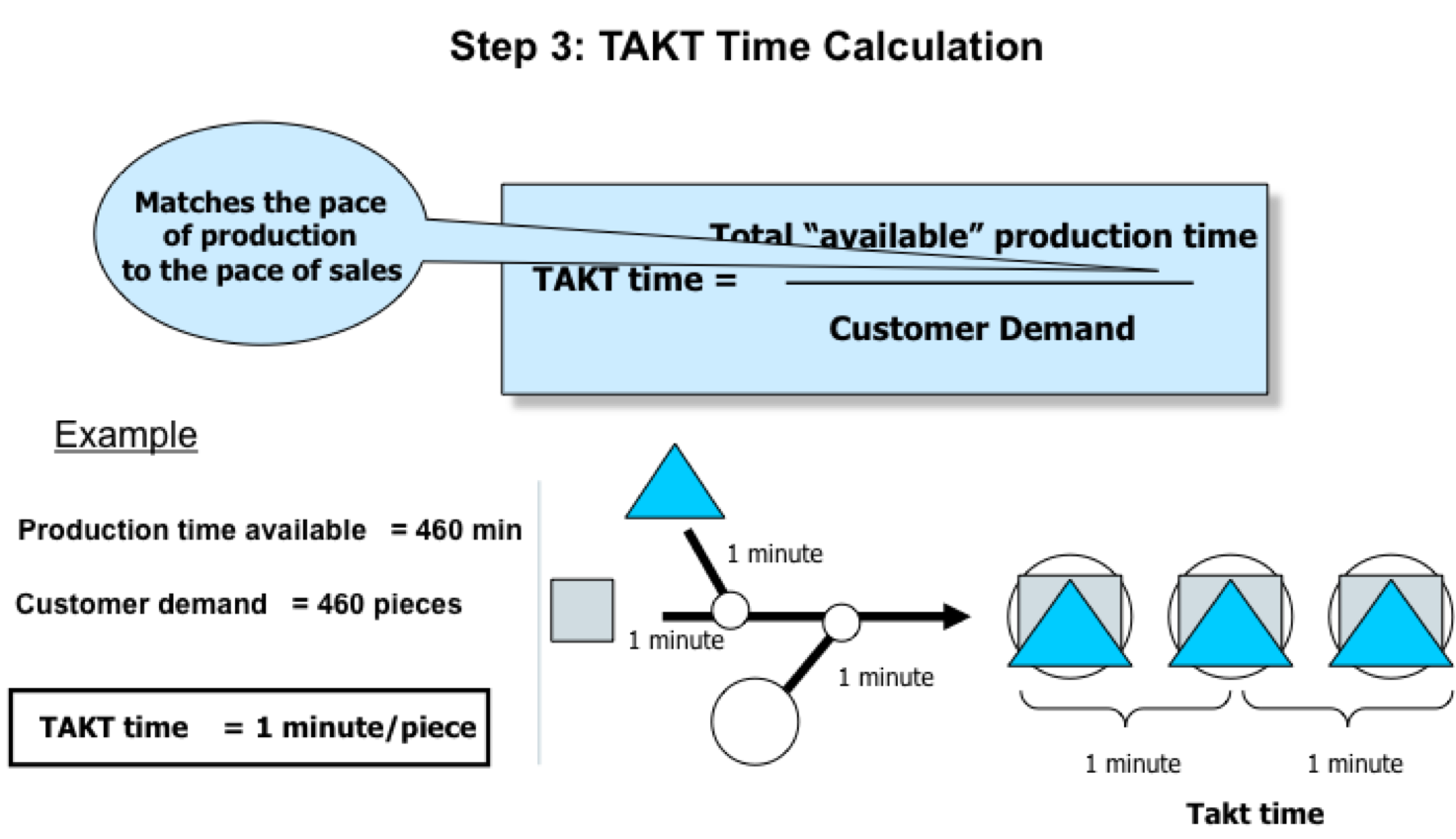
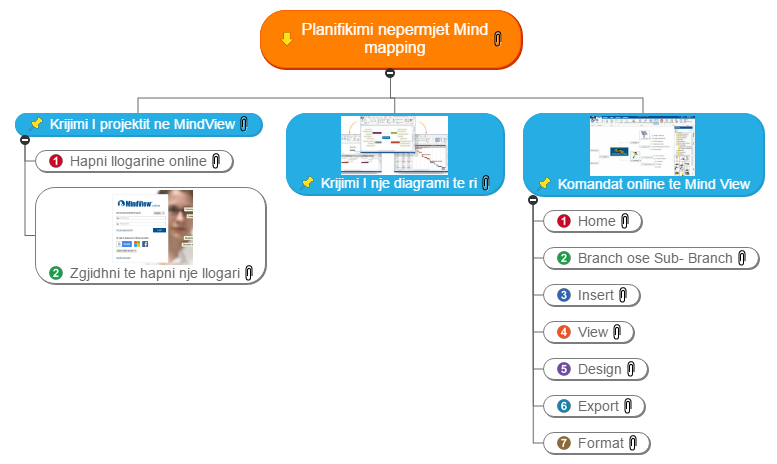
Motorola’s manufacturing business first used the strategy to identify and reduce process defects and keep a low variability of its manufacturing processes. The Six Sigma process improvement method dates back to the 1980s. Taiichi Ohno, Industrial engineer and Businessman, Considered to be the father of the Toyota Production System “The key to the Toyota way and what makes Toyota stand out is not any of the individual elements - but what is important is having all the elements together as a system.” Thus, the building blocks of Lean are its two pillars: respect for all people and continuous learning and improvement. In addition, to build an organizational culture, the concept suggests letting the people drive the change. The Lean management methodology originates from Lean manufacturing, established by Toyota in the late 1940s to reduce all non-value-adding activities from the work process.Īt the heart of the Lean management methodology lie three clear values: deliver from your customers’ perspective, eliminate all workflow waste, and continuously improve. Let’s find out more about the two approaches individually. Lean Six Sigma is the smart combination of the Lean methodology focused on removing waste and optimizing flow, while the Six Sigma method seeks to identify and remove causing issues. At its core, it is a process improvement approach for eliminating inefficiencies and improving work processes by identifying the defects’ root causes.
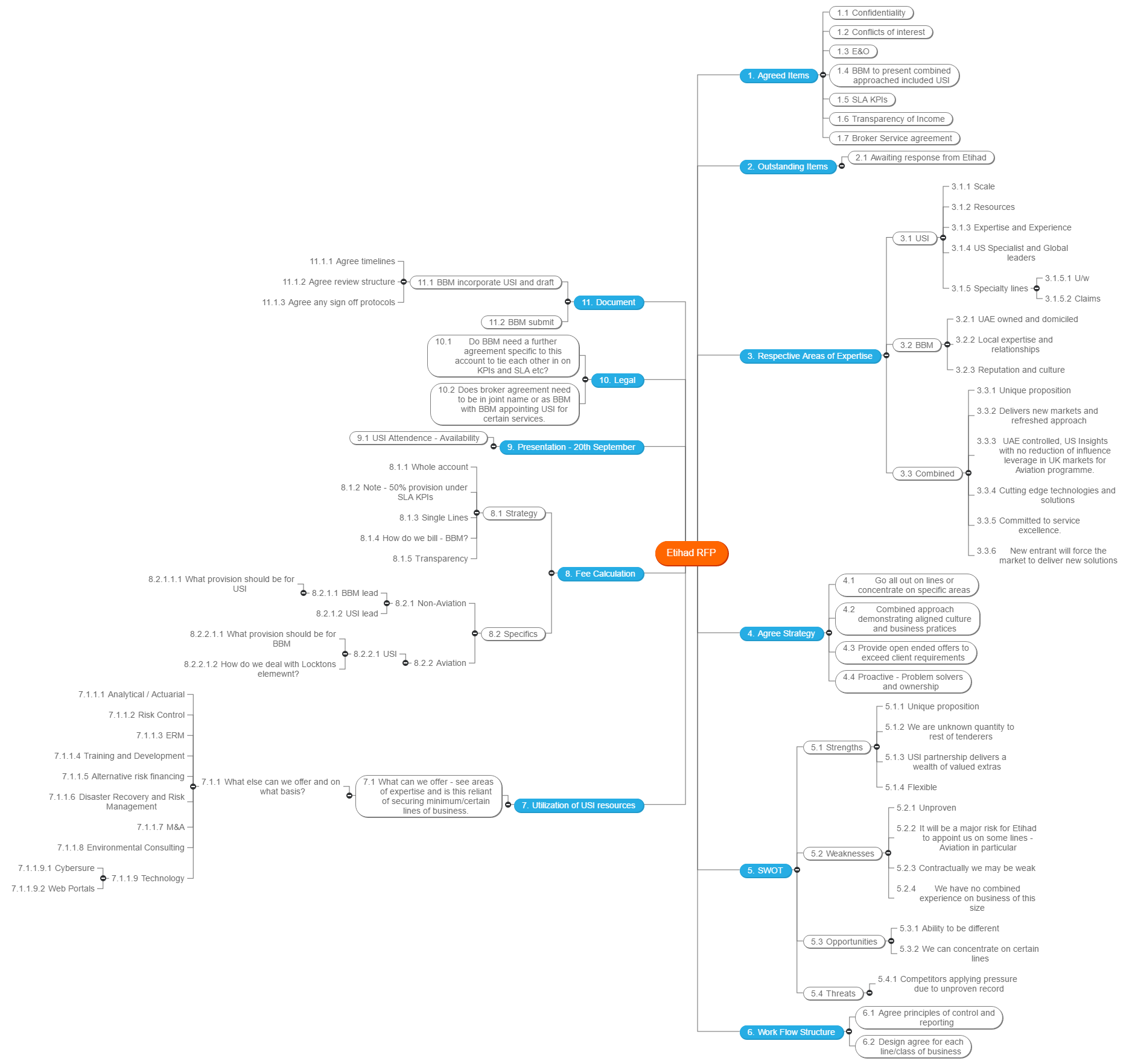
Lean Six Sigma represents a methodology for overall organizational culture change.
#Mindview 6 lean sigma update#
Integrate with external systems to get the most out of your Kanban softwareĬreate and update cards via email and reply to emails by adding a comment Reduce multitasking, alleviate bottlenecks, and keep a steady flow of work Visualize and track cross-team dependencies via card linksĬreate probabilistic plans for future project deliveryĪutomate your process to trigger actions when certain events occurĪnalyze your workflow’s performance through a variety of Lean/Agile charts Implement OKRs and align your strategy with day-to-day executionĭisplay critical business metrics and gather reports in one placeĬustomize your work items as needed and enhance communication

Visualize your past, current, and future initiatives or projectsĭistribute and track work across the entire organization Keep your teams' work in a single place with multi-layered Kanban boards Keep track of tasks and get accurate status reports in real-timeĬreate a network of interlinked Kanban boards on a team and management level
